OUR CAPABILITIES
- Casting
- Stamping
- Forging
- Tube Bending
- Metal Welding
- Lathe and Milling Processing
- Finishing
- Injection Molding
- Wire Harness & Cable Assembly
- Custom Sub-Assembly
Casting
Casting is a manufacturing process in which molten metal is poured into a mold and allowed to cool and solidify, forming the desired shape. It is widely used for producing various metal components.
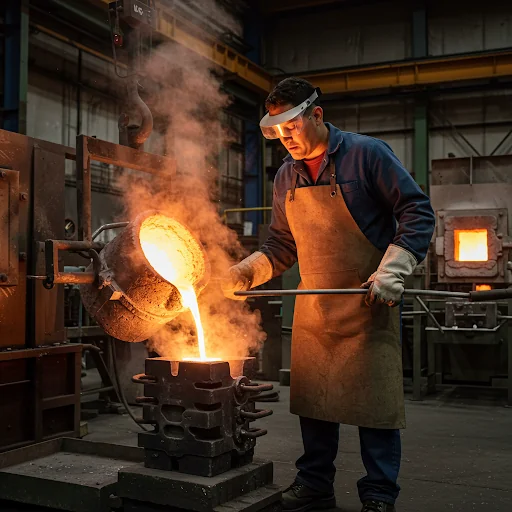
Common Casting Methods:
- Sand Casting: Uses sand as the mold material, making it suitable for large and complex-shaped castings. It is cost-effective and highly flexible, but the surface finish is relatively rough.
- Die Casting: Injects molten metal into a metal mold under high pressure, ideal for mass production with high dimensional accuracy and smooth surfaces. However, it is mainly suitable for low-melting-point metals such as aluminum, zinc, and magnesium.
- Investment Casting: Utilizes a wax mold to create precise and detailed components. It is ideal for manufacturing small, complex parts with high precision, commonly used in industries such as aerospace, medical, and high-end machinery. However, it is relatively costly.
Stamping
Stamping is a manufacturing process that applies external force to metal sheets using stamping dies and presses, causing plastic deformation or separation to achieve the desired shape and size. This technique is widely used in the automotive, electronics, home appliance, and metal product industries due to its efficiency, precision, and cost-effectiveness.
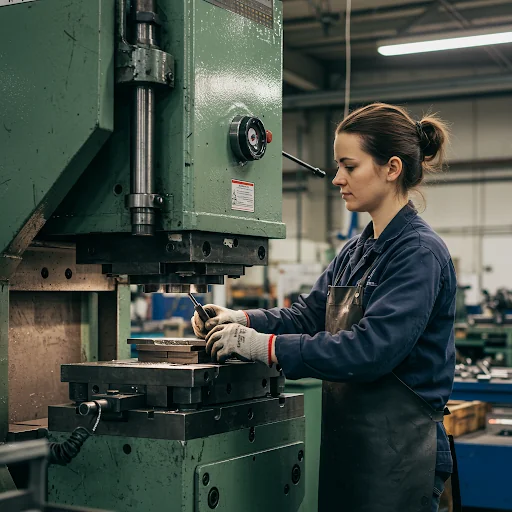
Common Stamping Processes:
- Punching: Uses a die to cut holes in metal sheets, commonly applied to ventilation holes, mounting holes, and other perforated designs.
- Shearing: Cuts metal sheets along a straight line, often used for material pre-processing or cutting sheets into specific dimensions.
- Deep Drawing: Stretches flat sheet metal into hollow shapes through a die, such as cups, cans, or other deep-drawn container components.
- Bending: Forms metal sheets into specific angles or shapes using a die, commonly used for frames, brackets, and structural components.
Forging
Forging is a manufacturing process in which external force is applied to metal through hammering or pressing, causing plastic deformation to achieve the desired shape and size. This process enhances the internal structure and mechanical properties of the metal, making it widely used for producing high-strength components.
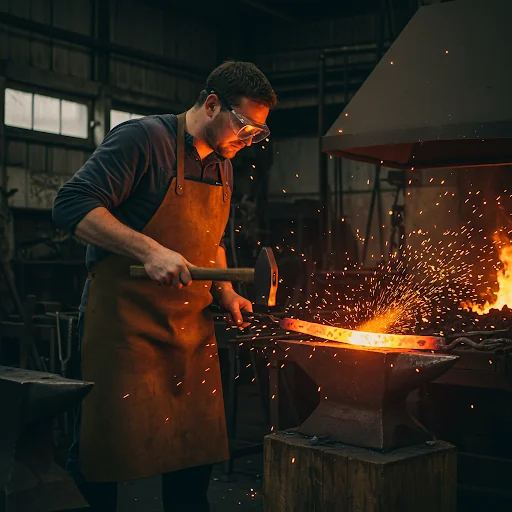
Common Forging Methods:
- Hot Forging: Performed at high temperatures, allowing better metal ductility and plasticity. It is suitable for large or complex-shaped components, such as those used in the automotive, aerospace, and heavy machinery industries.
- Cold Forging: Conducted at room temperature, providing high dimensional accuracy, a smooth surface finish, and increased metal strength. It is ideal for small to medium-sized parts, such as bolts, gears, and connectors.
- Open Die Forging: Uses no fixed molds and forms the shape through free hammering. It is suitable for large, single-piece, or small-batch production, such as shafts, rings, and special mechanical components.
- Closed Die Forging: Utilizes fixed molds to shape the metal, ensuring high consistency in part dimensions. It is ideal for mass production and is commonly used in the manufacturing of automotive, tool, and machinery components.
Tube Bending
Tube bending is a manufacturing process that applies external force through specialized equipment or molds to bend tubular materials into the desired angles and shapes. This technique is widely used in industries such as automotive exhaust systems, furniture, aerospace structures, construction supports, and commercial kitchen equipment.
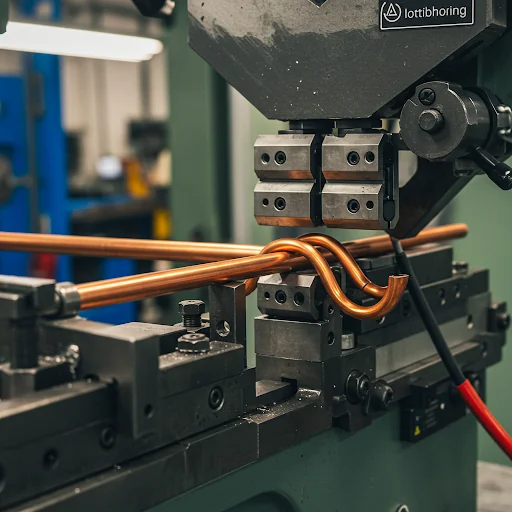
Common Tube Bending Methods:
- Press Bending: Uses a press die to apply direct pressure on the tube, making it suitable for large-radius bends. It is commonly used in structural frames and piping systems.
- Roll Bending: Utilizes rolling dies to perform continuous bending, ideal for long tubes with curved shapes, such as construction supports, railings, and large pipe manufacturing.
- Draw Bending: Combines dies and mandrels to precisely control the bending angle, making it suitable for small-radius, high-precision bends, such as automotive exhaust pipes, hydraulic tubing, and aerospace piping systems.
Metal Welding
Welding is a manufacturing process that joins metal materials permanently by applying heat, pressure, or a combination of both. This technique is widely used in construction, machinery manufacturing, automotive, aerospace, piping, and commercial kitchen equipment to ensure structural strength and durability.
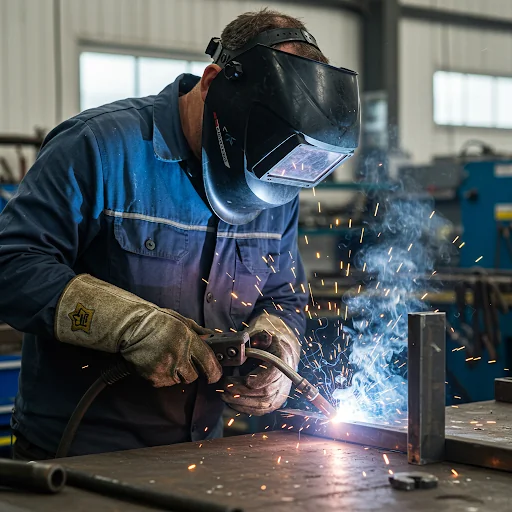
Common Welding Methods:
- Arc Welding: Uses the high temperature generated by an electric arc to melt and fuse the electrode with the workpiece. It is suitable for various metals and is widely used in structural construction and heavy industry manufacturing.
- Gas Welding: Uses the combustion of oxygen and acetylene to generate high temperatures for melting and joining metals. It is ideal for thin metal sheets and repair welding, such as in pipeline maintenance and craft fabrication.
- TIG Welding (Tungsten Inert Gas Welding): Uses inert argon gas to shield the arc, preventing oxidation in the weld area. It offers high welding precision and is suitable for aluminum, stainless steel, and applications requiring fine-quality welding, such as aerospace and medical equipment manufacturing.
- Resistance Welding: Generates heat through electrical resistance as current passes through the workpieces, fusing the metals together. A common type is spot welding, which is widely used for automotive body panels, electrical enclosures, and mass production of metal mesh structures.
Lathe and Milling Processing
Lathe and milling are two primary machining processes that remove material using cutting tools to achieve the desired shape and dimensions. These techniques are widely used in mechanical manufacturing, automotive parts, aerospace engineering, and precision equipment industries.
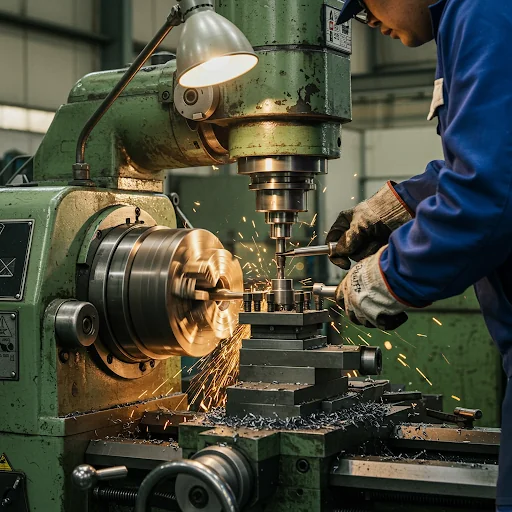
Machining Methods:
- Lathe Turning: Involves rotating the workpiece while the cutting tool moves along the axial or radial direction to shape it. This method is suitable for cylindrical components such as shafts, rings, and flanges.
- Milling: Uses a multi-tooth milling cutter to remove material, making it ideal for machining flat surfaces, grooves, inclined planes, and complex geometric shapes, such as mechanical parts, molds, and precision components.
- CNC Machining: Utilizes a computer numerical control (CNC) system to precisely control tool movement, allowing for high-precision and complex-shaped parts. It improves production efficiency and consistency, making it widely used in aerospace, medical devices, and high-end manufacturing industries.
Finishing
Finishing is a process that enhances the surface properties of a workpiece through chemical or physical methods, improving corrosion resistance, wear resistance, and aesthetics. This technique is widely used in mechanical manufacturing, automotive, aerospace, electronics, and commercial kitchen equipment industries to enhance durability and appearance.
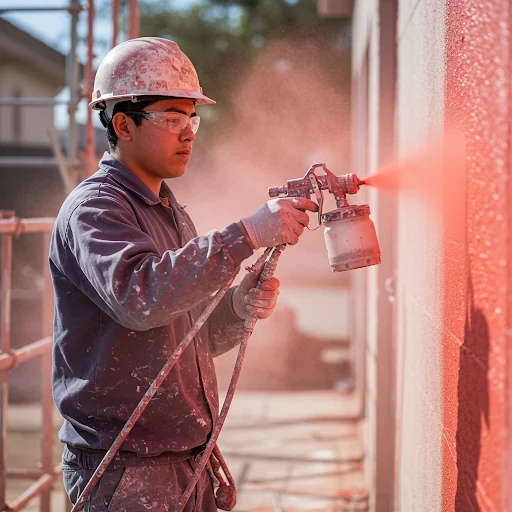
Common Finishing Methods:
- Polishing: Uses abrasives or polishing materials to remove surface roughness, creating a smooth and glossy finish. It is commonly applied to stainless steel, aluminum alloys, and various metal products.
- Plating: Deposits a thin metal layer, such as nickel, chromium, or zinc, onto the workpiece surface to enhance corrosion resistance, conductivity, and visual appeal. It is widely used in electronic components, tools, and decorative parts.
- Coating: Applies paint or powder coatings to provide protection and aesthetic enhancement. This method is used in industrial equipment, home appliance casings, and metal products for rust prevention and improved appearance.
- Anodizing: An electrochemical process that forms an oxide layer on metals such as aluminum or titanium, increasing corrosion resistance, hardness, and color variety. It is commonly used in aerospace, electronic enclosures, and high-end decorative components.
Injection Molding
Injection molding is a manufacturing process in which plastic is melted at high temperatures and injected into a mold under high pressure. Once cooled and solidified, the material forms a specific shape. This technique is widely used in automotive components, electronic enclosures, medical devices, and commercial kitchen equipment due to its high efficiency, large-scale production capability, and precision.
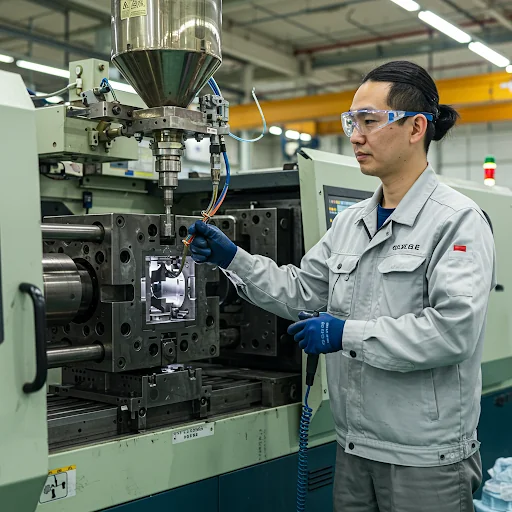
Common Molding Methods:
- Melting & Plasticizing: Plastic pellets are heated until they reach a molten state, ensuring good flowability for injection into the mold.
- Injection & Filling: The molten plastic is injected into the mold under high pressure, filling all details of the mold cavity to ensure a complete and accurate shape.
- Cooling & Solidification: The plastic cools and solidifies inside the mold, stabilizing the shape and ensuring dimensional accuracy and structural strength.
- Post-Processing: Additional treatments such as trimming excess material, drilling, coloring, and surface finishing are applied to enhance the quality and appearance of the final product.
Wire Harness & Cable Assembly
Wire harness and cable assembly is a process that involves arranging, securing, connecting, and bundling electrical wires, cables, and connectors according to design specifications. This ensures stable and reliable electrical connections. The technique is widely used in automotive, industrial equipment, medical devices, aerospace, and commercial kitchen equipment industries.
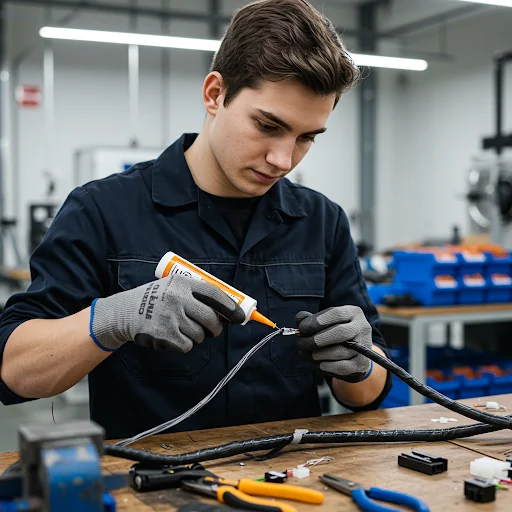
Wire Harness & Cable Assembly Process:
- Cutting: Precisely cutting wires or cables to the required length to ensure consistency in assembly.
- Stripping: Removing the outer insulation layer of the cable to expose the conductor for terminal connection or soldering.
- Crimping: Using crimping techniques to securely attach terminals to wires, ensuring stable electrical transmission and mechanical strength.
- Bundling: Securing wire harnesses using ties, sleeves, or heat shrink tubing to maintain a neat arrangement and prevent loosening or interference.
- Testing: Conducting continuity, insulation, and voltage withstand tests to ensure the safety and reliability of wire harnesses and cables.
Custom Sub-Assembly
Custom sub-assembly is the process of pre-assembling parts or subcomponents according to customer requirements to enhance production efficiency and streamline the final product assembly. This technique is widely used in industrial equipment, electronics, automotive components, medical devices, and commercial kitchen equipment industries.
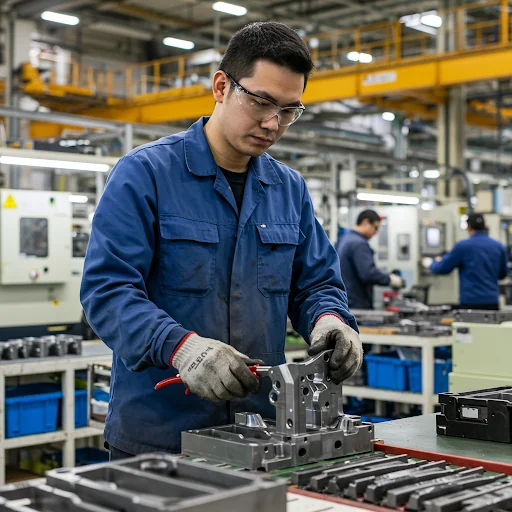
Custom Sub-Assembly Process:
- Parts Inspection: Ensuring all parts meet dimensional tolerances and quality standards to improve assembly accuracy and reliability.
- Pre-Assembly: Assembling parts in advance according to design specifications to enhance efficiency and reduce assembly errors.
- Function Testing: Conducting performance tests on sub-assemblies to ensure they meet specifications and operate reliably.
- Packaging & Delivery: Packaging products securely based on customer requirements to ensure safe transportation and timely delivery.
OUR MISSION
Castaly Enterprise Corp. is committed to delivering competitive, total-cost solutions tailored to your procurement needs for OEM parts. For over 40 years, we have upheld the highest standards of integrity and transparency, dedicating ourselves to quality and service excellence. As a result, we have become the most trusted long-term partner of globally renowned commercial kitchen equipment manufacturers.
We specialize in the precise customization of metal parts, consistently providing competitive pricing, exceptional quality, and reliable on-time delivery. Choose Castaly as your preferred partner for OEM metal parts in the commercial kitchen equipment industry.
INDUSTRIES WE SERVE
CONTACT US
Looking for OEM parts made in Taiwan? Please complete the order form below and upload any product drawings, specifications, or materials lists you have. Thank you!